How to Become a Safety Manager
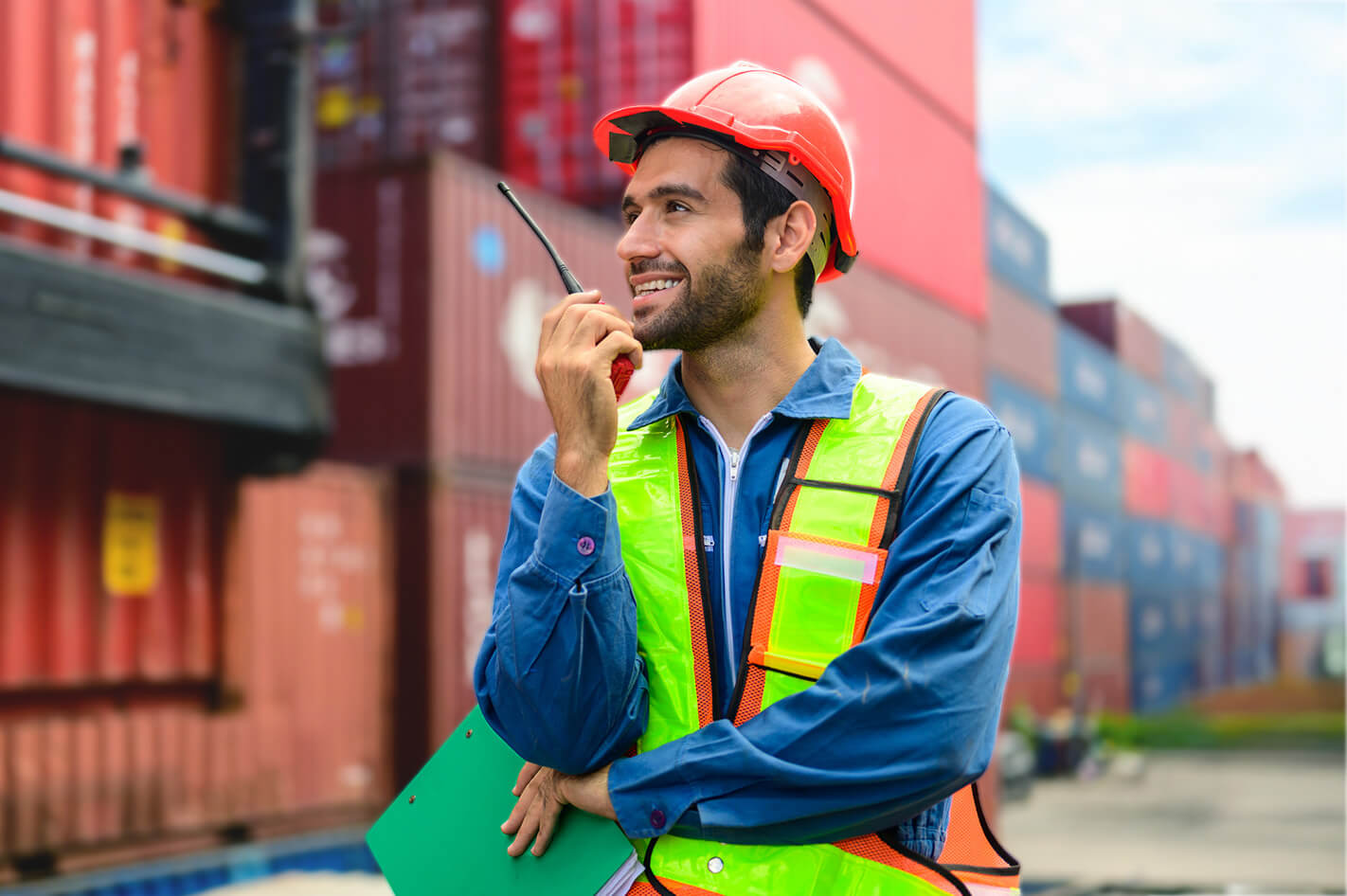
The work of a safety manager can be fulfilling as you get to promote and improve safety in your workplace. However, it’s not always an easy job, and getting qualified can be challenging without the right credentials. You must consider whether you have the right traits, if you plan to get a degree, which industry to get into, what area of concentration you should focus on, and budget for the required training programs. This guide details what you need to prepare for.
What Is a Safety Manager?
Safety managers are professionals who keep a workplace safe and free from risks or hazards. They have a deep understanding and a vested interest in health and safety principles. They check that safety regulations are strictly followed, keeping equipment and personnel compliant. To help minimize accidents and injuries, they also help design safe systems in the workplace. They perform daily inspections and safety audits to ensure systems are implemented according to specific regulations or consensus standards.
Safety managers may be the point of contact for other government agencies, companies, or organizations involved in health and safety (consider EPA, DOT, local fire departments, and municipal government). They’re also typically familiar with the industries they work in. For instance, a certified safety manager in construction may have a construction-related degree, such as engineering or architecture.
What Does a Safety Manager Do?
A safety manager’s roles and responsibilities can vary depending on the job. Your responsibilities will also depend on your level of seniority. However, your main priority would be to help avoid workplace injuries and illnesses. As stated by the Occupational Safety and Health Administration (OSHA), no employee should become ill, injured, or die for a paycheck. Your company will also appreciate your help in avoiding legal battles resulting from safety violations.
Here are the main responsibilities of a safety manager:
- Assess risks and hazards: You assess your work environment for potential risks and hazards due to equipment or your processes. Depending on your position, you may have to notify management of these hazards and suggest ways to lessen them. If you find yourself in a more senior role, you may also review and approve inspection and audit reports.
- Ensure strict compliance with safety standards: Whether it’s a standard from OSHA, the American National Standards Institute (ANSI), or a local jurisdiction, inspect your workplace at least annually to ensure compliance, including reviewing your workplace for fire safety compliance.
- Evaluate and update systems and processes: If you find that some processes or systems in the workplace need to be adjusted based on your review, you can persuade employers and your colleagues to adopt better and safer practices and protocols. You may need to change your budgets, work systems, or management priorities.
- Develop a plan for emergencies: You need to have an emergency response plan in place. It can be challenging to have zero accidents, so it’s essential to have protocols in place for what to do in the event of one. You can perform drills, so everybody knows what to do in these situations. You should also ensure that emergency equipment is always available.
- Train and educate all employees: As a safety manager, you should be able to train and educate all employees regardless of seniority level. Managers and supervisors, in particular, need to know how to adopt effective safety practices. Training can also promote a culture of safety and help reduce accidents.
- Investigate and analyze accidents: Once an incident occurs, you’ll need to analyze reports related to it and evaluate the situation, including conducting a root cause analysis and implementing corrective actions. Obviously, the purpose of a thorough investigation is to identify how to prevent the issue from recurring.
- Maintain and manage a safety database: You must record all incidents and manage a safety database for your company. The safety database can include training sessions, inspection reports, maintenance records, and other safety-related documentation.
- Collaborate with external agencies: You can request expert consultations or partner with government agencies, state departments, or private companies to enhance safety in your workplace.
Safety Manager Qualifications
Similar to the roles and responsibilities, requirements to become a safety manager also vary per industry and jurisdiction. Training and certification may be required. Some companies or agencies may also require specific courses. Course requirements depend on your experience level. You may also need to renew your license regularly, typically, every three years.
You can expect other usual requirements such as:
- You should be at least 18 years old.
- You should be able to read and write English.
- You should have a good moral character.
Essential Skills of a Safety Manager
A safety manager’s job is crucial, as having them on site keeps workers safer. However, to be an effective safety manager, you need to possess a specific set of traits.
These qualities will help you out:
- Detail-oriented: Because you’ll be inspecting the work area regularly, you should be able to spot risks and hazards that may not always be obvious. Even a small detail can pose a significant risk if overlooked. Additionally, complex safety standards require your attention to detail to ensure your workplace complies.
- Problem-solver: You must be able to prevent a hazard from turning into an accident and identify ways to prevent an incident from recurring. What’s more, emergencies require you to quickly decide how you will solve the problem. The job entails observing, analyzing, and solving problems through decision-making.
- Technical and innovative: Technical skills are essential if your industry involves working with equipment or machinery. Having a background or related degree can give you an edge. You could be testing equipment or identifying ways to improve its safety.
- Physically fit: A safety manager does not get a desk job. You should be able to be on your feet for long periods and act quickly and according to protocol when necessary. A true safety professional will spend time “in the field”, discussing safety issues and opportunities with workers and seeking their input.
- Communicative: You must communicate effectively with management, co-workers, and other agencies. Strong communication skills are essential for effectively communicating safety instructions and issues to various parties.
Safety Manager Education Requirements
You don’t always need a degree to be a safety manager. Sometimes, a high school diploma or equivalent is enough. However, a college degree can reduce the required experience for some jobs and is a requirement for some certifications. The knowledge you’ll earn from a degree can also be beneficial. For instance, a degree can teach you about related laws, safety and inspection, and management. Degrees may be required in specific industries, such as chemistry, engineering, or biology.
If you’re unsure what to study, a degree in occupational health and safety can help you become a safety manager. However, a degree in a related field might be best. For instance, a degree in construction management can help you become a construction safety manager. If you’re looking for more senior roles, you may need a master’s degree.
Relevant Experiences
Even if a degree is not required, relevant experience might be. For instance, in New York, a college degree is not required, but you need at least five years of relevant experience in the construction industry.
Entry-level jobs can help you gain this experience. You may also get trained on fall protection, hazardous materials, monitoring equipment, and workspace inspections, even as a junior employee. On-the-job training is highly regarded in the safety industry.
How to Become a Safety Manager
Once you’ve identified that you have the essential skills, education requirements, and relevant experience needed, you’re now more equipped for the next steps. To become a certified safety manager, you’ll need training and certification. This certification is typically required and dependent on the nature of your industry. The timeline depends on the length of your program. Here are the steps you need to take.
1. Review Relevant Training Programs
Many training programs are available for safety managers, and they can be done online or in person. Each program targets a specific set of skills. The length of each program also varies. It can be as quick as a 24-hour training program or one that can take 242 hours to finish. You can train for professional development, but there are also specialist courses and training for trainers.
Whichever program you choose, ensure that it meets OSHA’s training requirements. OSHA has specific standards for certain industries, such as maritime and construction. There are general industry requirements as well. Employers must also train their employees in these safety standards. Apart from OSHA, ANSI has its own standards and criteria for training programs. They specifically highlight guidelines for e-learning in safety, health, and environmental courses.
Depending on your program, you may learn about:
- Emergency action plans
- Fire prevention plans
- Occupational noise exposure
- Powered platforms for building maintenance
- Explosive and blasting agents
- Flammable liquids
- Proper storage and management of gases and chemicals
- Hazardous waste operations
- Confined space entry
- Electrical and lockout tagout
Site-specific programs are based on the needs of your site or work environment. After your training, you should receive written documentation, such as a certificate and a laminated card, which can serve as proof of training. The card may include your identification number for the training certificate.
2. Choose Your Certification
You don’t always need a certification to be a safety manager. However, it is required in some instances, and can give you an edge in the hiring process if you have one. Certifications are also available, whether you’re fresh out of college or looking to advance your career. Once you become a safety manager, you can continue to develop your skills by taking on additional certifications.
The National Association of Safety Professionals (NASP) is here to help you progress toward your goals as a safety professional. We offer online certification exams for the MSP and CSD certifications, which are two of the best safety certifications you can strive toward.
- Master Safety Professional (MSP)®: An MSP is someone who possesses high-level strategic and specialist skills. MSPs often participate in developing and implementing facility-wide health and corporate safety programs and carry influence with policymakers and senior management personnel. They consider the broader social and organizational contexts that impact safety and health to create comprehensive solutions for their organizations.
- Certified Safety Director (CSD)®: CSDs solve problems and apply safety strategies for organizations. They offer advice based on their extensive training, which provides them with technical and conceptual knowledge. They’re experts at analyzing evidence and critically thinking to find solutions. CSDs have an evidence base that helps them provide value in professional collaboration settings. They can work with very little supervision and are often the ones providing direction and supervision to others in a workplace setting.
We also offer online safety courses to provide the education you need throughout your career. Here are some examples of certificate courses you can take (with or without a degree):
- Certified Safety Manager: Construction (CSMC): This certificate showcases that you know the safety policies and processes typical in the construction industry. Some of what you can learn includes relevant regulations, how to minimize injuries, and how to increase worker morale.
- Certified Safety Manager (CSM): CSM proves that you’ve learned the essential knowledge and skills for safety within the business industry. Like CSMC, you can also learn about relevant regulations, how to increase morale, and how to avoid or minimize injuries in the workplace.
- Psychological Health and Safety Manager Certificate (PHSM): PHSM enables you to design and manage your company’s Psychological Health and Safety program. You can learn about the various principles developed by many research professionals and the psychosocial hazards and risks in the workplace.
- Safety Auditor Certificate (SAC): Because a safety manager’s role involves a lot of observation and analysis, the SAC can help by providing a deeper understanding of hazard analysis, inspections, and investigations.
- ADA Compliance Certificate: Complying with the Americans with Disabilities Act (ADA) is essential to ensure your workplace does not discriminate against people with disabilities. With this compliance certificate, you’ll be able to spot issues and make improvements on-site.
- OTI Courses: OSHA Training Institute 500/510 for Construction and 501/511 for General Industry (you must have a minimum of five years of experience in safety to qualify).
3. Take the Exam
After you go through the courses, you can expect an online exam with a required passing rate. For instance, you may need an 80% passing rate to receive your certificate. Expect that you can take the exam only a specific number of times. Once you have earned your certificate, you may need to take a refresher course and exam, typically after every three years.
Is It Hard to Become a Safety Manager?
It can be challenging to become a safety manager if you don’t have the necessary skills or credentials. Safety manager jobs that don’t require a college degree, certification, or relevant experience can be easier to get. However, the lack of requirements won’t make the actual work easier — instead, it can be harder due to a steeper learning curve.
A safety manager is a serious role, as your capabilities can determine how many accidents and injuries a workplace has. It’s possible to succeed in the industry given the training and certifications available.
Safety Managers at Work
When thinking about becoming a safety manager, managing your expectations and learning about what your day-to-day can look like can be helpful.
Work Environment
The work environment varies depending on your industry. A business work environment will likely be less hazardous than a factory. Safety managers are also typically found in construction sites, hospitals, warehouses, and government settings. Wherever you find yourself, you can expect that your work will require extensive fieldwork and exposure to potentially stressful situations. You’d need to be alert to your surroundings.
Salary Expectations
The average salary of a safety manager in the United States is about $89,000 annually. The lowest salary can be about $60,000, with the highest ones reaching $133,000. Wages vary based on the location and nature of your job. Having certifications can also boost your salary.
Level up With the National Association of Safety Professionals
The National Association of Safety Professionals (NASP) can help you increase your opportunities as a safety manager by improving your skill set. Whether you plan to train for the government, oil and gas, or the general industry, we have the training and professional certifications to help you. Our training meets multiple regulatory requirements. Depending on the certification you choose, we also meet and exceed OSHA and ANSI standards. You can take the courses in person or online.
We believe in promoting a safe culture beyond regulatory compliance. Our main driving force is to help you do whatever is necessary to keep your work environment safe and free from accidents. Review our training programs today to get started!